Visit to Unipart Advanced Logistics Centre
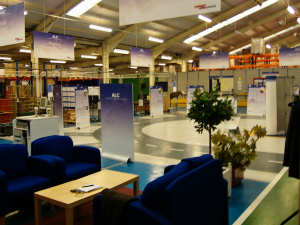
In a departure from our usual meeting location in the centre of Oxford, over 30 people travelled to Unipart’s global Head Office on the outskirts of Cowley to learn about how they are using technology, including RFID, to improve logistics processes for their customers.
Unipart is one of Europe’s leading independent providers of third party logistics and distribution services. It was formed after a management and employee buy-out from British Leyland in 1987 and has developed into a major international company with a turnover of £1.2bn. It employs over 10,000 staff and focuses on the Manufacturing, Rail, Automotive, Leisure & Marine and Logistics & Business Services sectors. Unipart has been a pioneer of the Lean operating system originally developed in Japan by Honda and Toyota. The company culture is one of continuous process improvement and although many organisations claim to follow this, it really did seem intrinsic to Unipart’s ways of working. As part of this, it was interesting to note that "Our Contribution Counts" quality circles had saved Unipart over £5.5m so far. Unipart was now providing process consultancy services to a number of major customers outside of the Logistics area, including a major government department.
After an introduction to Unipart from Gareth Jenkins, Sales Director, in the Unipart Conference Centre, we made our way across the site to the Advanced Logistics Centre where Phil Wood, Head of Systems Practice, explained how Unipart used this facility to model the physical logistics processes for customers and worked with them on improvement. This facility could be configured to physically model each of the steps in the supply chain from manufacture to retail shop sales. Of particular interest to the audience was the use of RFID to improve picking accuracy, tracking distribution and controlling stock. RFID "tags" could be applied to containers, pallets, roll cages, boxes or individual items according to the customer requirements. Tags could be passive (only read by a reader) or active (emitting a radio signal) and could be used for different ranges for different applications. They also came in different form factors including paper labels and nails that could be hammered into wood.
It was clear from the visit that there are many applications for RFID but to really take advantage of the technology required a detailed understanding of how the supply chain processes could be improved and the careful selection of the right solution.